Automazione e domotica negli impianti industriali: verso la fabbrica intelligente
Immagina un’officina dove le macchine non solo producono pezzi, ma comunicano tra loro, anticipano i propri guasti e regolano autonomamente il consumo energetico dell’intero edificio. Immagina un magazzino dove le luci si accendono solo dove serve, la temperatura è sempre ottimale per la conservazione dei materiali e la sicurezza è gestita da un sistema intelligente che distingue un dipendente da un intruso.
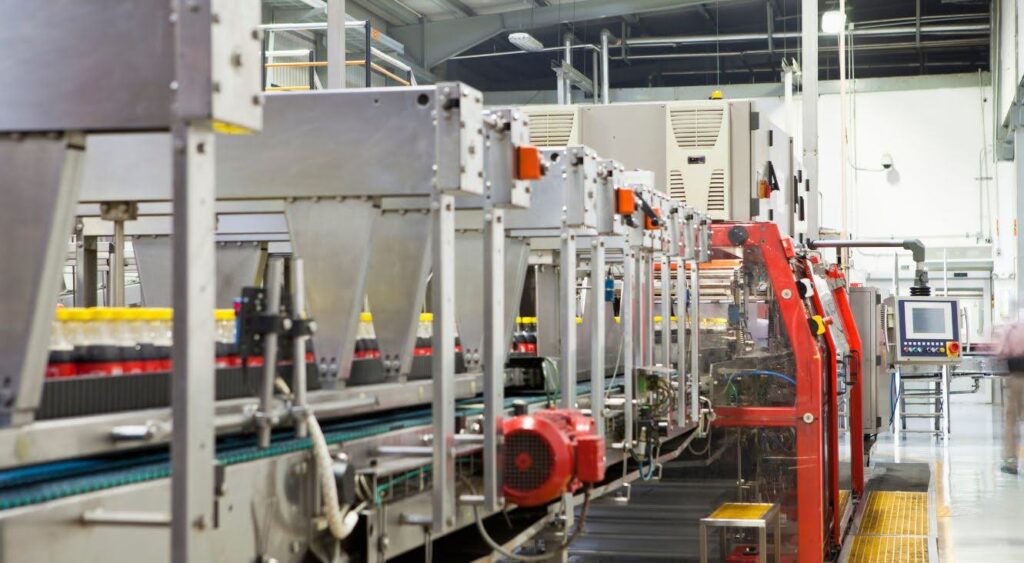
Fantascienza? No, è la realtà della fabbrica intelligente, o Smart Factory, un concetto che sta rivoluzionando il settore manifatturiero dalle fondamenta. E al centro di questa trasformazione ci sono due forze motrici potentissime: l’automazione avanzata e un’applicazione specializzata della domotica.
In questo articolo, ti accompagnerò in un viaggio alla scoperta di come queste tecnologie stiano convergendo per creare stabilimenti più efficienti, sicuri e sostenibili. Non parleremo solo di robot e bracci meccanici, ma di un ecosistema connesso che sta cambiando per sempre il modo di produrre e gestire un impianto industriale.
Facciamo chiarezza: non solo robot, ma cervelli digitali
Quando si parla di automazione industriale, l’immagine che salta alla mente è spesso quella di un braccio robotico che assembla automobili. È corretto, ma è solo una piccola parte della storia. L’automazione moderna è molto di più.
Ma andiamo con ordine. L’automazione industriale è l’uso di sistemi di controllo – come computer, robot e tecnologie informatiche – per gestire macchinari e processi industriali, sostituendo l’intervento umano. L’obiettivo è sempre stato quello di aumentare la produttività e ridurre i costi.
Oggi, però, siamo entrati in una nuova era, quella dell’Industria 4.0. I pilastri di questa rivoluzione sono:
- PLC (Controllore Logico Programmabile): Il “cervello” di una macchina o di una linea di produzione. È un computer industriale robusto che esegue istruzioni specifiche in tempo reale.
- SCADA (Supervisory Control and Data Acquisition): Pensa a una sorta di “ponte di comando” digitale. I sistemi SCADA raccolgono dati da tutti i PLC e sensori sparsi per l’impianto e li presentano su un’interfaccia grafica, permettendo agli operatori di monitorare e controllare l’intero processo da una postazione centrale.
- DCS (Sistema di Controllo Distribuito): Simile allo SCADA, ma usato in processi più complessi e continui (come nelle raffinerie o negli impianti chimici), dove ogni sezione dell’impianto ha un proprio controllore dedicato che coopera con gli altri.
Questi sistemi esistono da decenni. La vera magia avviene quando li connettiamo a tecnologie più recenti, come l’Internet of Things (IoT) e l’intelligenza artificiale (AI). Ed è qui che un concetto, preso in prestito dal mondo residenziale, trova un’applicazione industriale sorprendentemente efficace: la domotica.
Dalla casa all’industria: il ruolo degli impianti domotici nella fabbrica
Siamo abituati a pensare alla domotica come a un sistema per gestire le luci, le tapparelle e il riscaldamento di casa con lo smartphone. Ora, prova a traslare questo concetto su una scala molto più grande e complessa: un intero stabilimento industriale.
Ecco dove entra in gioco un concetto che potremmo definire “domotica industriale” o, più tecnicamente, Building Automation. Non si tratta più solo di controllare la linea di produzione, ma di gestire in modo intelligente l’edificio stesso, integrandolo con i processi produttivi.
Gli impianti domotici in un contesto industriale non gestiscono le tapparelle, ma si occupano di:
- Gestione Energetica: Monitoraggio in tempo reale dei consumi di ogni singolo macchinario e area. Il sistema può spegnere automaticamente le luci nelle zone vuote, regolare la climatizzazione in base all’effettiva necessità e persino decidere di avviare i processi più energivori nelle fasce orarie a minor costo.
- Climatizzazione e HVAC (Heating, Ventilation, and Air Conditioning): Mantenere temperature e umidità stabili è cruciale in molti settori (alimentare, farmaceutico, elettronico). Un sistema intelligente lo fa in modo proattivo, ottimizzando i consumi e garantendo la qualità del prodotto.
- Sicurezza e Controllo Accessi: Sistemi di videosorveglianza intelligenti, capaci di riconoscere anomalie, integrati con il controllo degli accessi per sapere sempre chi è presente in ogni area dello stabilimento.
- Manutenzione Predittiva dell’Edificio: Sensori che monitorano lo stato delle infrastrutture (impianto idraulico, elettrico, di ventilazione) e segnalano la necessità di un intervento prima che si verifichi un guasto.
L’integrazione tra l’automazione di processo e la domotica industriale crea un ecosistema dove la fabbrica non è più un contenitore passivo, ma un partecipante attivo ed efficiente nel processo produttivo.
I pilastri tecnologici della Fabbrica Intelligente
Questa convergenza è resa possibile da alcune tecnologie chiave che lavorano in sinergia:
- Internet of Things (IoT): In parole povere, si tratta di dare un’identità digitale agli oggetti fisici. Sensori a basso costo vengono installati su macchinari, componenti, scaffalature e persino sull’edificio stesso. Questi sensori raccolgono dati di ogni tipo (temperatura, vibrazione, posizione, consumo energetico) e li trasmettono in rete.
- Big Data e Analytics: La mole di dati generata dall’IoT è enorme. I sistemi di Big Data sono in grado di raccogliere, immagazzinare e processare queste informazioni. Gli Analytics, poi, cercano schemi, correlazioni e anomalie, trasformando i dati grezzi in informazioni preziose.
- Intelligenza Artificiale (AI) e Machine Learning: L’AI è il motore che analizza i dati e prende decisioni. Gli algoritmi di Machine Learning “imparano” dai dati storici. Ad esempio, possono imparare a riconoscere le vibrazioni anomale di un motore che precedono un guasto, attivando un allarme di manutenzione predittiva.
- Cloud Computing: Fornisce la potenza di calcolo e lo spazio di archiviazione necessari per gestire tutto questo, senza dover investire in costosi server fisici in azienda. Permette di accedere ai dati e controllare l’impianto da qualsiasi luogo.
I vantaggi concreti: perché un’azienda dovrebbe investire?
Tutto questo suona fantastico, ma quali sono i vantaggi tangibili per un’azienda manifatturiera? Perché un imprenditore dovrebbe avviare un percorso di trasformazione così profondo? I motivi sono solidi e misurabili.
- Efficienza Operativa e Produttiva: Le macchine lavorano a ciclo continuo con una precisione irraggiungibile per l’uomo. I fermi macchina vengono ridotti drasticamente grazie alla manutenzione predittiva. L’intera catena del valore, dalla ricezione delle materie prime alla spedizione del prodotto finito, viene ottimizzata.
- Riduzione dei Costi: Meno sprechi di materiale, minor consumo energetico, riduzione dei costi di manutenzione (si interviene solo quando serve), ottimizzazione del personale. L’investimento iniziale viene ammortizzato da risparmi significativi e costanti nel tempo.
- Qualità Superiore e Meno Errori: I sistemi di visione artificiale e i controlli automatizzati possono ispezionare il 100% della produzione, scartando i pezzi difettosi con una precisione millimetrica. Il risultato è uno standard qualitativo più elevato e costante.
- Maggiore Sicurezza sul Lavoro: Le mansioni più pericolose, ripetitive e faticose vengono delegate ai robot. Gli operatori umani possono concentrarsi su compiti di supervisione, controllo e programmazione in un ambiente di lavoro più sicuro.
- Flessibilità e Personalizzazione: La fabbrica intelligente può essere riprogrammata rapidamente per passare dalla produzione di un lotto a un altro, anche per piccole quantità. Questo permette di rispondere in modo agile alle richieste di un mercato che chiede sempre più prodotti personalizzati (la cosiddetta “mass customization”).
Un capitolo fondamentale: l’efficienza energetica e la sostenibilità
Un aspetto spesso sottovalutato, ma di importanza strategica cruciale, è l’energia. Una fabbrica intelligente è, per definizione, una fabbrica energeticamente efficiente. La gestione domotica dei consumi è il primo passo, ma la vera svolta è l’autoproduzione.
Qui si inserisce un tassello fondamentale: l’energia rinnovabile. Integrare un sistema di automazione e domotica con un impianto di produzione energetica, come quello fotovoltaico, crea un circolo virtuoso. La fabbrica non solo consuma meno, ma produce da sé una parte significativa (o la totalità) dell’energia di cui ha bisogno, pulita e a costo zero dopo l’ammortamento dell’impianto.
Non è un caso che la richiesta di impianti domotici a Brescia, Mantova, Bergamo, Verona e tutto il nord Italia da parte delle aziende manifatturiere sia in costante crescita. In un’area ad alta densità industriale, l’indipendenza energetica e la riduzione dell’impronta di carbonio non sono più solo scelte etiche, ma veri e propri vantaggi competitivi. Un sistema domotico intelligente può gestire i flussi energetici, decidendo se utilizzare l’energia prodotta dai pannelli, immagazzinarla in sistemi di accumulo o prelevarla dalla rete quando il costo è inferiore.
L’elemento umano: da operatore a supervisore
Una delle paure più grandi legate all’automazione è la perdita di posti di lavoro. È una preoccupazione legittima, ma la storia ci insegna che le rivoluzioni tecnologiche non eliminano il lavoro, lo trasformano.
Nella fabbrica intelligente, il ruolo dell’essere umano si evolve. Le competenze richieste cambiano:
- Meno lavoro manuale e ripetitivo.
- Più competenze digitali: capacità di interagire con software complessi, interfacce uomo-macchina (HMI) e sistemi di analisi dati.
- Problem solving: capacità di interpretare i dati forniti dalle macchine per risolvere problemi complessi e ottimizzare i processi.
- Supervisione e manutenzione specializzata: servono tecnici in grado di programmare, gestire e manutenere robot e sistemi automatizzati.
L’operaio diventa un “supervisore di processo”, un ruolo a più alto valore aggiunto. La sfida per le aziende e per il sistema formativo è quella di investire nell’aggiornamento delle competenze (upskilling e reskilling) per preparare la forza lavoro a queste nuove professioni.
Come iniziare? I primi passi verso la tua Fabbrica Intelligente
La transizione verso una fabbrica intelligente può sembrare un’impresa colossale, ma non deve essere fatta in un solo passo. È un percorso graduale. Ecco alcuni consigli pratici per iniziare:
- Analisi e Visione: Parti da un’analisi approfondita dei tuoi processi attuali. Dove sono i colli di bottiglia? Dove si concentrano i costi e gli sprechi? Quali sono le aree più critiche? Definisci una visione chiara di ciò che vuoi ottenere.
- Inizia in Piccolo (Progetto Pilota): Non cercare di automatizzare tutto subito. Scegli un’area specifica o una singola linea di produzione per un progetto pilota. Questo ti permetterà di testare le tecnologie, misurare i risultati e imparare dagli errori con un rischio controllato.
- Focalizzati sui Dati: Inizia a raccogliere dati. Anche solo installare sensori per monitorare i consumi energetici o i fermi macchina può fornire insight incredibilmente utili per giustificare investimenti futuri.
- Scegli i Partner Giusti: Affidati a system integrator e consulenti con comprovata esperienza nel tuo settore. La scelta del partner tecnologico è cruciale per il successo del progetto.
- Coinvolgi e Forma il Tuo Team: La tecnologia da sola non basta. La trasformazione deve essere compresa e abbracciata da tutto il personale. Comunica la visione, spiega i benefici e investi nella formazione fin dalle prime fasi.
Esempi pratici di ROI e miglioramenti operativi
Caso studio settore automotive
Un produttore di componenti automotive di medie dimensioni ha implementato una soluzione completa di smart factory che includeva celle di assemblaggio automatizzate, monitoraggio qualità in tempo reale con sistemi di visione, manutenzione predittiva per le apparecchiature critiche e un sistema di esecuzione manifatturiera (MES) integrato. L’implementazione è stata graduale su 18 mesi con un investimento totale di 4,2 milioni di dollari. I risultati ottenuti entro due anni dal completamento dell’implementazione hanno mostrato un ritorno completo sull’investimento con miglioramenti specifici: riduzione del 37% dei difetti di produzione, diminuzione del 28% dei tempi di inattività non pianificati, miglioramento del 22% nell’efficacia complessiva delle apparecchiature (OEE) e riduzione del 15% dei costi di produzione.
Efficienza energetica e sostenibilità
L’azienda Henkel, in collaborazione con partner tecnologici, ha implementato una soluzione di efficienza completa che includeva PLC, EMS, Big Data e sviluppo OEE. Il sistema EMS include circa 4.000 sensori fisici e virtuali che raccolgono oltre un milione di punti dati al giorno in 27 fabbriche nel mondo. La riduzione del consumo energetico annuale è stata fino al 18% nel 2021. L’investimento in processi più sostenibili e apparecchiature di automazione ha mostrato un payback completo in quattro anni, con un ROI quadruplicato dopo otto anni e miglioramenti dell’efficienza delle apparecchiature del 15% dopo soli due anni.
Impatto della manutenzione predittiva
La manutenzione predittiva rappresenta uno dei benefici più significativi dell’automazione industriale. I team di manutenzione possono utilizzare l’analisi predittiva per aumentare l’uptime delle apparecchiature fino al 20%. Molte organizzazioni riportano costi di downtime compresi tra 100.000 e 300.000 dollari per ora o più.
Le ricerche indicano che il 95% degli adottanti della manutenzione predittiva ha riportato un ROI positivo, con il 27% di questi che ha ottenuto l’ammortamento in meno di un anno. Il costo mediano del downtime non pianificato in 11 settori industriali è di circa 125.000 dollari per ora.
Miglioramenti operativi misurabili
Studi recenti sui sistemi di produzione intelligenti mostrano miglioramenti significativi in diversi indicatori chiave di performance. Le metriche di automazione mostrano un guadagno medio del 10% nel grado di automazione, una riduzione dell’11% nei tempi di inattività e un aumento del 3% nell’efficienza energetica.
Le metriche di efficienza dei processi evidenziano una riduzione significativa dei tempi di ciclo di 18 secondi, una diminuzione dei tassi di difetto dell’1,3% e un aumento della produttività di 25 unità per ora. I risultati complessivi mostrano un aumento del 2% nell’efficienza complessiva delle apparecchiature (OEE), una riduzione del 2,2% nel consumo energetico totale, una diminuzione del 20% nei difetti per migliaia di unità e un aumento del 4% nella produzione.
Il futuro è già qui
La fabbrica intelligente, alimentata dalla sinergia tra automazione avanzata e impianti domotici industriali, non è più una visione futuristica. È una realtà concreta e un’opportunità imperdibile per le aziende che vogliono rimanere competitive in un mercato globale sempre più esigente.
Significa produrre meglio, con costi inferiori e un impatto ambientale ridotto. Significa creare ambienti di lavoro più sicuri e stimolanti. Significa, in definitiva, trasformare il proprio stabilimento da un semplice luogo di produzione a un asset strategico, intelligente e proattivo. La strada è tracciata: abbracciare questa evoluzione non è più un’opzione, ma una necessità per prosperare nel futuro dell’industria.
Fonti principali
- IoT Analytics – “Mapping 4,000 global industrial automation projects” – Questa fonte fornisce un’analisi completa e aggiornata (2025) di oltre 4.000 progetti globali di automazione industriale, con dati specifici su implementazioni, settori e distribuzione geografica.
- Convergix Automation – “7 Manufacturing Automation Statistics and Key Takeaways” – Questa fonte offre statistiche chiave aggiornate al 2024 sulle tendenze dell’automazione manifatturiera, con proiezioni di crescita del mercato e impatti occupazionali.